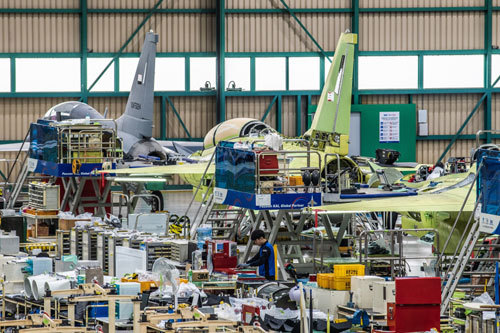
“자, 찢어보세요.”
지난 2일 경남 사천 한국항공우주산업(KAI) 본사 부품동 클린룸에서 항공기 동체에 사용되는 탄소 복합재를 만드는 과정을 소개하던 KAI 관계자가 검은색 절연테이프 같은 것을 건넸다.
테이프는 아무리 당겨도 늘어나지도 찢어지지도 않았다. 탄소 소재로 만들어진 카본 테이프였다.
이런 테이프를 수백장 붙여 고온·고압에서 가공하면 항공기 신소재로 각광받는 복합재가 만들어진다. 복합재는 기존에 항공기 동체 등에 많이 사용되던 알루미늄보다 무게가 70% 수준으로 가볍다. 그런데 강도는 더 높아 KAI가 자체 개발한 다이아몬드 절삭 장비를 써서 특수 가공해야 한다.

KAI 부품동에는 먼지 등 불순물이 복합재에 끼어드는 걸 막기 위해 외부와 철저히 차단된 클린룸이 7개 있었다. 각각의 룸에선 기계 설비를 이용한 대형 복합재, 근로자의 수작업을 통한 소형 복합재 생산이 한창이었다.
클린룸 안은 KAI의 핵심기술이 담겨 있어 대부분 외부에 공개되지 않는다. 수리온 헬기 블레이드가 만들어지는 클린룸이 대표적이다. 탄소섬유와 복합재 폼 등이 적용되어 개발된 블레이드는 KAI가 세계에서 10번째로 개발한 기술이다.
클린룸에서 만들어진 복합재 제품은 다양한 항공기 내·외부 구조물에 광범위하게 사용된다. 항공기에 복합재가 필요한 이유는 연료 효율 때문이다. 같은 연료를 채웠을 때 동체가 가벼우면 더 멀리 날아갈 수 있다. KAI 관계자는 “보잉의 B787-9, 에어버스 A350 기체 50% 이상이 복합재로 만들어진다”고 설명했다.
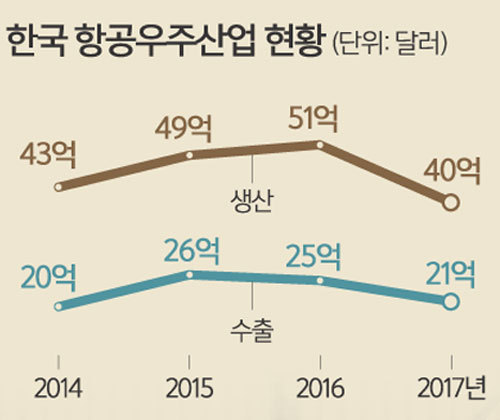
이날 부품동을 시작으로 한국 항공우주산업의 ‘메카’인 KAI를 속속들이 들여다봤다. 1999년 설립된 KAI는 2001년 한국 최초 항공기 수출 실적 KT-1 인도네시아 수출, 2010년 국산 헬기 수리온 헬기 초도비행 성공, 세계 6번째 초음속기 수출 2011년 T-50 인도네시아 수출 등 한국 항공산업 역사를 매번 바꿔 쓰는 회사다.
또한 KAI는 민항기 제조사 보잉과 에어버스의 대형 구조물 등을 제작하는 핵심 파트너다. 자체 기술로 군용기 성능개량 및 개조도 가능하다. KAI는 최근엔 항공기 정비사업(MRO), 무인기, 우주, 신사업 확장 등을 통해 2030년 매출 20조원 규모의 세계 5위 항공우주 체계종합업체로 도약을 준비 중이다.
이어 둘러본 조립동은 부품동에서 제작된 부품 구조물을 조립해 항공기의 동체, 날개 구조물을 제작하는 곳이다. 이날 생산되고 있던 구조물은 A321 항공기의 비상구 부분 동체였다. 4개의 패널을 연결해 제작되며, 3000여개의 부품과 나사 형태의 22000여개 리벳으로 구성된다.
B737-800 항공기의 수평·수직 꼬리날개(미익)도 있었다. B737 미익은 전체 물량 중 50%는 KAI에서, 나머지 50%는 중국에서 제작돼 미국 시애틀 보잉 공장에서 최종 조립된다.
조립동 한쪽에는 미군의 전투용 헬기 AH-64D 동체 구조물이 보였다. 블레이드와 엔진 등 일부를 제외한 AH-64D 동체 대부분은 KAI가 독점 생산한다. 2003년부터 지금까지 약 500여대가 납품됐다.
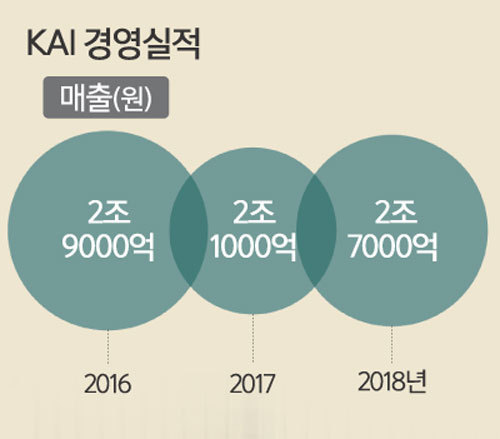
항공기 최종 조립단계인 항공기동은 축구장 3개 정도 규모로 컸다. 항공기동 최종 조립장 바닥에는 마그네틱 센서가 적용되어 있어 항공기 동체·날개구조물, 작업을 위한 자재 등이 자동 이동 로봇에 실려 현장에 배치된다. 이날 조립장에서는 T-50TH 태국 수출기와 마린온 상륙기동헬기, KT-1S 세네갈 수출기 등 국산 항공기의 최종 조립이 단계별로 진행됐다.
KAI에는 에어버스의 A350 항공기 주날개에 들어가는 뼈대 ‘윙립’을 만드는 별도의 전용공장 A350동도 있다. 이 공장에선 주날개에 들어가는 66개(날개당 33개)의 윙립 중 KAI가 대형 윙립 56개(날개당 28개), 협력업체가 소형 윙립 10개를 생산한다. A350 윙립은 KAI가 항공기 개발 단계부터 설계에 참여한 국제공동 개발 사업이다.
특히 A350동은 공정은 설계 단계부터 KAI 엔지니어들이 참여한 스마트 공장으로 자동화율이 87%에 달했다. KAI는 A350 스마트 공장 구축을 위해 2010년부터 2014년까지 약 1000억원을 투자해 공장을 건설했다. A350동은 보안이 매우 철저해 발주처인 에어버스 직원들에게도 잘 공개하지 않는다고 했다.
스마트공장의 성과는 혁신적이었다. 스마트 공정 구축으로 KAI는 종전에 2주가 걸리던 생산기간을 10분의 1 수준으로 단축했으며 단가도 낮췄다. A350동 관계자는 “이 공장은 주 1회 점검시간을 제외하고 24시간 가동이 가능하며, 향후 인공지능(AI) 기술 등을 활용하여 공정을 지속적으로 고도화하고 있다”고 말했다.
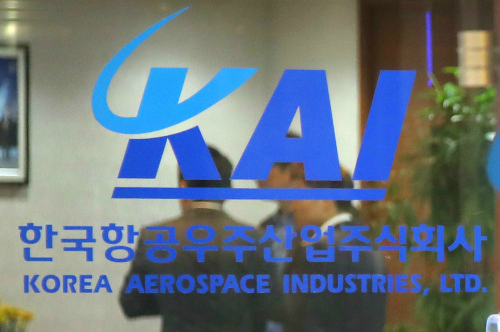
KAI의 사업영역도 점차 확장 중이다. KAI는 본사 옆 기존 2사업장을 지난해 MRO 전문 자회사인 한국항공서비스(KAEMS)에 출자했다. KAEMS는 국토교통부가 지정한 MRO 전문업체다. KAEMS는 지난 2월 제주항공 B737 여객기의 정비를 시작으로 국내 첫 저비용항공사(LCC) 정비를 시작했다. 기자가 방문한 이날은 이스타항공의 B737 여객기를 정비했다.
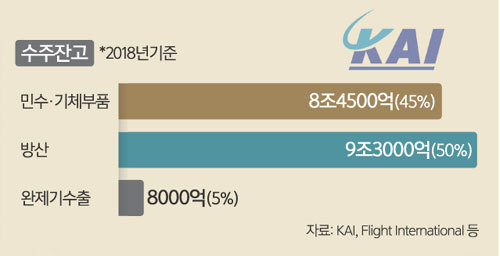
김태호 KAEMS 품질안전팀 부장은 “기체 중정비 착수로 현재 싱가포르, 중국, 몽골 등 해외에 위탁하고 있는 1조원 규모 물량의 국내 전환이 가능해 외화유출 절감효과가 있다”며 “LCC들은 또 해외 정비 대비 중정비 기준 2~3일을 단축할 수 있어 안정적인 운항 스케줄 관리가 가능해진다”고 강조했다.
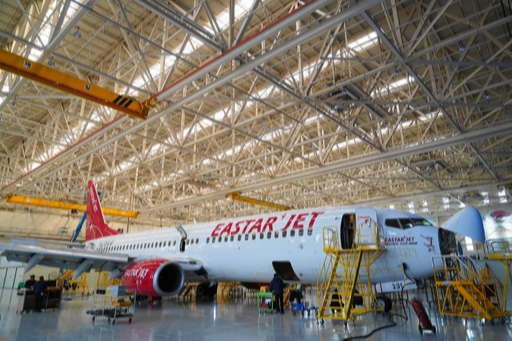
KAEMS의 일부 공간에서는 KAI의 군용기 성능개량과 정비 능력을 볼 수 있었다. 과거 KAI는 한국군에서 운용되고 있는 링스 헬기, HH-47, UH-60, P-3CK, F-16D 등의 항공기의 성능개량과 E-737 개조, 미군 태평양 함대 H-53 대형헬기의 정비 등의 다양한 사업을 수행했다. 이날도 미 공군의 F-16과 한국 해군의 P-3CK의 정비, 공군의 C-130 성능개량이 진행 중이었다.
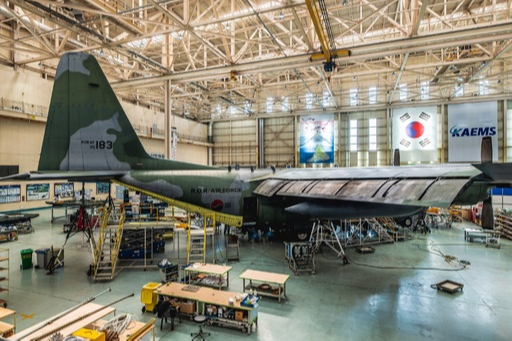
C-130은 미군에서 퇴역해 애리조나주의 사막지역인 이른바 ‘비행기 무덤’에 버려진 12대를 우리 군이 들여왔고, KAI가 이들을 껍데기 골격만 남기고 기체를 보강하고 최첨단 레이더 등을 장착해 특수 임무용으로 개조한다.
사천=나기천 기자 na@segye.com
[ⓒ 세계일보 & Segye.com, 무단전재 및 재배포 금지]