IT연구진·현장 베테랑 작업자들 공조
2016년 빅데이터 수집… 이듬해 딥러닝
2020년 세계 첫 열연 공정 통합운전실 구축
4차산업혁명 시대 흐름 선제 대응 평가
2300℃ 용광로 내부 상태 실시간 확인
불량률↓ 생산량 ↑… 포항·광양 4기 가동
제철소 전 공정 도입 목표로 연구 ‘박차’
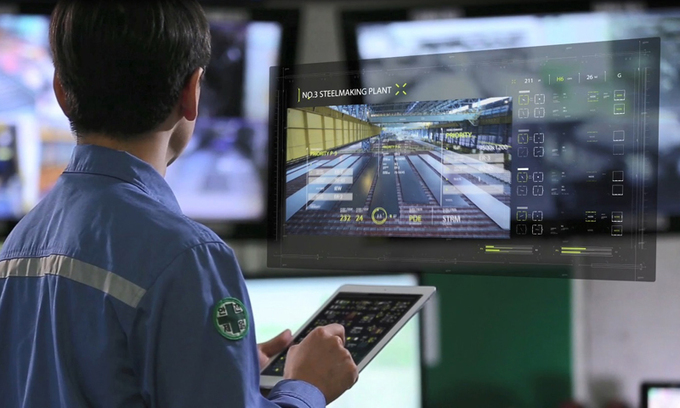
고로를 타고 흘러나오는 뜨거운 쇳물이 모니터를 통해 실시간으로 방영된다. 고로 원료인 코크스의 색깔과 상태가 실시간으로 관제실로 전송되고 고로는 자동으로 코크스 유입량을 결정한다. 포항제철의 제조공정이 진화해 조업자가 일정 시간마다 직접 고로 상태를 확인하던 시스템이 아닌 빅데이터를 기반으로 한 AI(인공지능) 시스템이 뜨거운 용광로로 들어왔다.
12일 찾은 경북 포항시 포스코 포항제철소 제2고로, 높이 100m에 내부온도 섭씨 2300도에 달하는 거대한 용광로가 시선을 사로잡는다. 뜨거운 액체와 고체가 뒤섞여 안을 들여다볼 수 없는 수준이지만, 거대한 용광로 내부 온도와 상태 사진이 실시간으로 3층 통합운전실로 전송된다. 통합운전실에서는 실시간으로 전송된 각종 데이터들을 토대로 고로 조업을 자동으로 제어한다.
기자의 눈에 비친 2고로는 이제 철을 만들어내는 용광로의 모습이 아닌 기술을 녹여낸 용광로로 비쳤다. ‘AI용광로’라고 불리는 포항제철의 제2고로는 제선 현장에서 30년 이상 근무한 베테랑들의 노하우가 녹아있는 스마트용광로다. 글로벌 철강 분야 기술 1인자 답게 포스코의 신기술이 집약된 포항제철소 2고로는 일일 용선 생산량 240t, 연간 8만5000t을 추가 생산할 수 있도록 경쟁력을 강화했다.
지금까지 통신과 포털, 각종 IT(정보기술) 기업들의 전유물로만 여겨졌던 빅데이터와 AI 기술이 스마트팩토리를 통해 고도화된 철강 제조공정에 녹아드는 일은 쉬운 일이 아니었다.
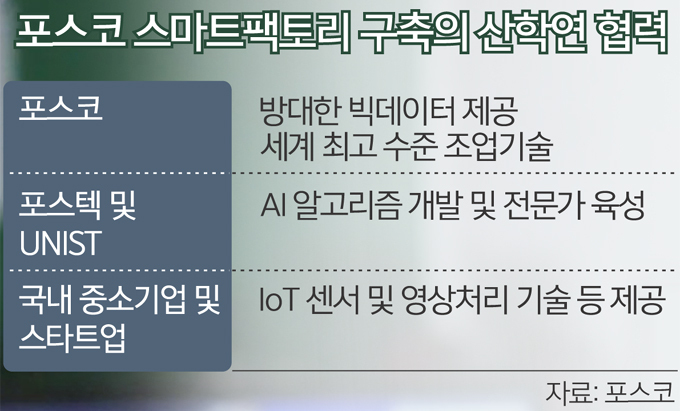
포스코의 스마트팩토리 시스템이 단순 자동화를 넘어설 수 있었던 것은 빅데이터와 IoT(사물인터넷), AI 시스템 등 3가지 빅테크 기술이 집약됐기 때문이다. 연구진과 현장의 공조를 통한 빅데이터를 기반으로 정밀한 IoT 센서가 조업 상황을 실시간으로 통합운전실에 전송하면, AI 시스템이 이를 분석해 최적의 조업으로 자동제어한다.
포스코의 AI 용광로는 수많은 변수와 사례를 학습하고, 연·원료의 성분과 용광로 상태를 스스로 점검한다. 이를 바탕으로 조업 결과를 미리 예측한 뒤 조업 조건을 선제적으로 자동 제어한다. 그 결과 품질 편차가 작은 최고의 산출물(쇳물)을 결괏값으로 뽑아낸다. 포항 2고로를 포함해 광양 3고로 등 포스코는 포항과 광양에 각각 2기씩 총 4기의 스마트 고로를 구축 또는 가동하고 있다.
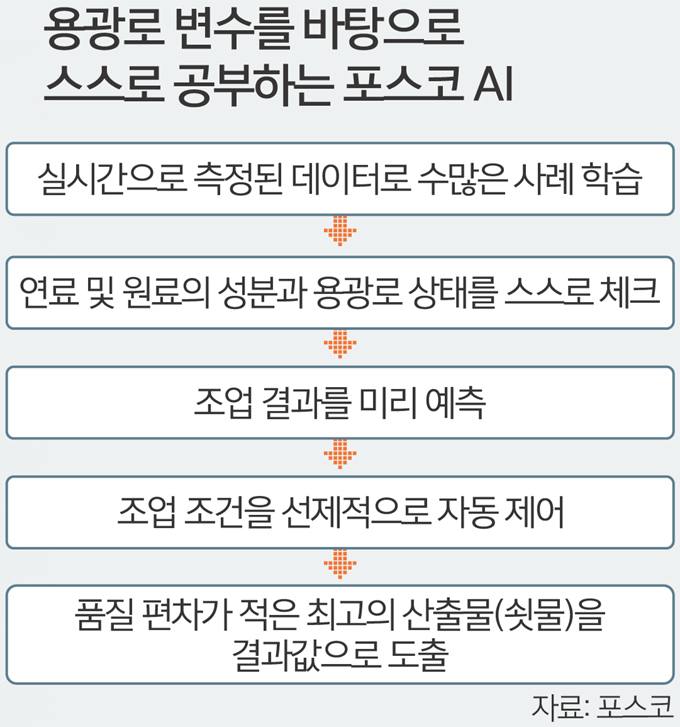
이 중 포항제철소 2고로는 4차 산업혁명 기술의 집약체다. 포스코는 4차 산업혁명이라는 키워드가 꿈틀거리던 2016년, 곧장 숙련도에 의지해 관리하던 용광로의 각종 지표를 모두 정형화하고, 데이터화하는 용광로의 ‘디지타이제이션(digitization)’에 착수했다. 모든 시작은 빅데이터였다. 코크스 주입에 따른 용광로 상태 등 수십가지 변수를 반영한 수만장의 사진이 빅데이터 초석이 됐다. 연구진은 노하우를 가진 베테랑 기술자들과 함께 고난도 분류작업을 이뤄냈고, 그 결과 포스코는 2017년부터 수많은 사례를 학습하는 딥러닝을 시작했다. 알아서 변수를 제어하고, 최적의 결괏값을 산출할 수 있도록 하는 ‘스마타이제이션(smartization)’이 본격 추진됐다.
포스코는 2020년 7월, 세계 최초로 열연 전 공정에 스마트 기술을 적용하여 한곳에서 컨트롤할 수 있는 통합운전실을 구축했다. 기존에는 압연된 소재를 두루마리 형태로 돌돌 말아주는 권취 공정의 운전실이 분리되어 있어 작업 효율이 떨어졌지만 인공지능을 적용해 품질 편차를 획기적으로 줄였다. 압연 공정은 조업 상황에 따라 최적의 압연량을 자동 설정해 주는 스마트 기술로 제품 손실을 크게 줄였다. 열연 전 공정이 스마트팩토리화되어 통합운전실에서 컨트롤되는 것은 포스코 포항제철소가 세계 최초 사례다.
글로벌 기업들이 스마트팩토리를 표방하고 있지만 포스코의 스마트팩토리가 특별한 이유는 ‘연속 공정’이라는 제철소의 특수한 조건에 최적화한 시스템을 구축했기 때문이다. 포스코는 용광로뿐 아니라, 일관제철공정의 전반에 스마트팩토리를 확산했다.
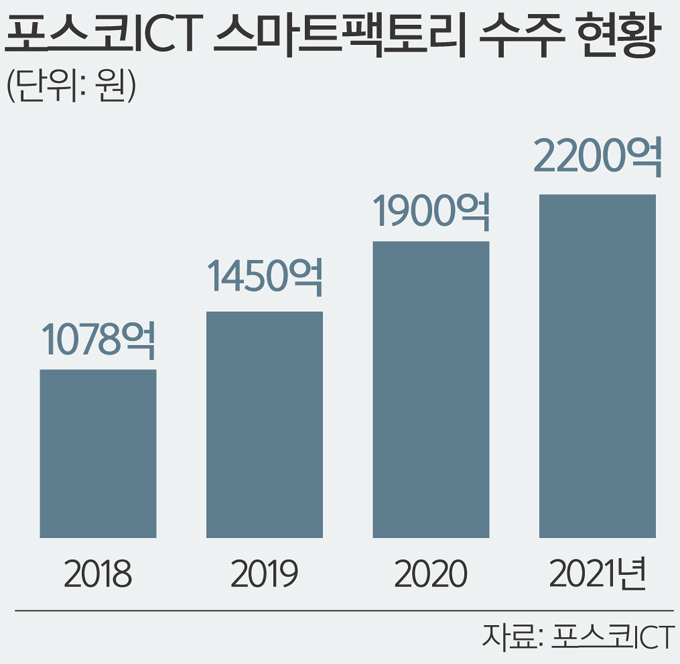
포스코 스마트팩토리의 엔진인 ‘포스프레임’을 통해 생산계획에서부터 최종 제품을 고객사에 인도하는 전 과정이 스마트팩토리로 이뤄진다. 여의도 3배가 넘는 포항제철 부지에 있는 수백 개의 공장, 수백 가지 강종에 대한 생산 정보를 한 곳에 모으고 누구나 가공할 수 있게끔 정형화·데이터화하는 것이 포스프레임의 주요 기능 중 하나다.
포스코가 스마트팩토리를 통한 경쟁력 강화에 성공한 것은 시대적 흐름을 미리 읽어냈기 때문이다. 노동인구 고령화로 인한 숙련공 부족과 맞춤형 소량생산 체제, 제품 라이프 사이클 단축 등의 이슈에 대응하기 위해 스마트화 필요성이 꾸준히 제기돼 왔고, 코로나19를 경험하면서 제조업의 리쇼어링(국내 복귀) 추세와 맞물려 이러한 흐름이 더욱 가속화되고 있다. 그룹사인 포스코ICT도 포스코를 지원해 제철소 스마트팩토리 추진 노하우를 활용하여 국내 제조업을 대상으로 확산을 추진하고 있다. 포스코ICT는 LS니꼬동제련, 풍산, 동화기업 등의 스마트팩토리를 추진했다.
이 같은 스마트팩토리를 사용하는 데도 포스코만의 의식이 녹아 있다. 기술이 인간의 대척점이 있는 게 아니라 인간을 위한 기술을 실현한다는 것이 포스코의 AI 철학이다. 포스코 관계자는 “결국 현장의 노련한 조업자들이 보다 정확한 판단을 할 수 있도록 기술이 도와주는 것”이라며 “작업자들은 하루 종일 용광로를 바라보며 상태를 관리하는 대신 보다 창의적인 업무에 집중할 수 있다”고 설명했다. 이에 포스코는 기술 개발뿐만 아니라 기술을 이용하는 직원들에 대한 AI 교육에도 열을 올리고 있다. 직원들의 데이터 분석·관리 등 IT 신기술 활용능력 향상을 위해 AI 활용 전문가 교육과정 기회를 현장 엔지니어들과 직원들에게 제공하는 등 인력 양성에 힘을 쏟고 있다.
지난 2019년부터는 제철소 전 공장을 스마트팩토리로 바꾸기 위해 추진조직을 재정비해 확대시켰으며, 현재는 기존의 개별 공정 최적화를 넘어서 공정 통합 또는 공정 관통형 과제를 추진하고 있다. 연속공정으로 이루어진 제철소의 특성상 단위설비나 단위공정 등 부분 최적화가 아닌 전체 최적화를 추진하고 있는 것이다. 포스코가 지난해까지 추진한 스마트 과제는 총 600여건이며, 기대이익은 2900억원 수준에 이를 것으로 예상하고 있다.
포항=김건호 기자 scoop3126@segye.com
[ⓒ 세계일보 & Segye.com, 무단전재 및 재배포 금지]